Robotic Welding
The Future of Precision and Efficiency
Robotic welding refers to the use of automated machines, often controlled by computers or artificial intelligence, to perform tasks with precision and consistency. This technology has revolutionized manufacturing and fabrication by increasing productivity, reducing errors, and improving workplace safety. As industries strive for efficiency and cost savings, robotic welding is becoming a key player in modern production processes.
How Does Robotic Welding Work?
At its core, robotic welding comprises robotic arms equipped with welding tools that follow programmed instructions to join metal components. Sensors and cameras often integrate with these machines to ensure accuracy. Artificial intelligence or pre-programming allows them to adapt to a variety of welding needs for repetitive tasks. Some advanced systems use real-time monitoring that allows adjustments on the fly to optimize weld quality.
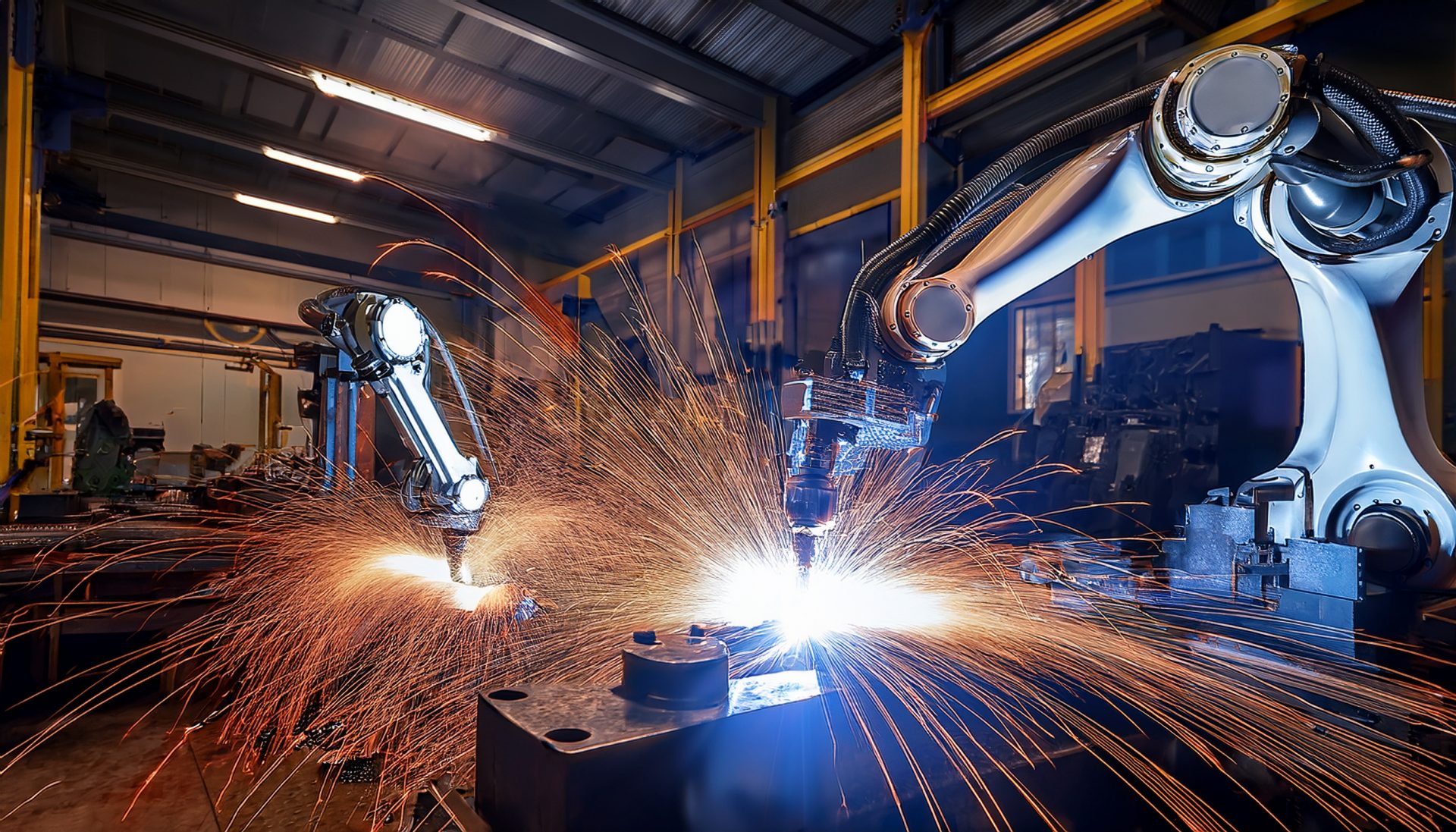
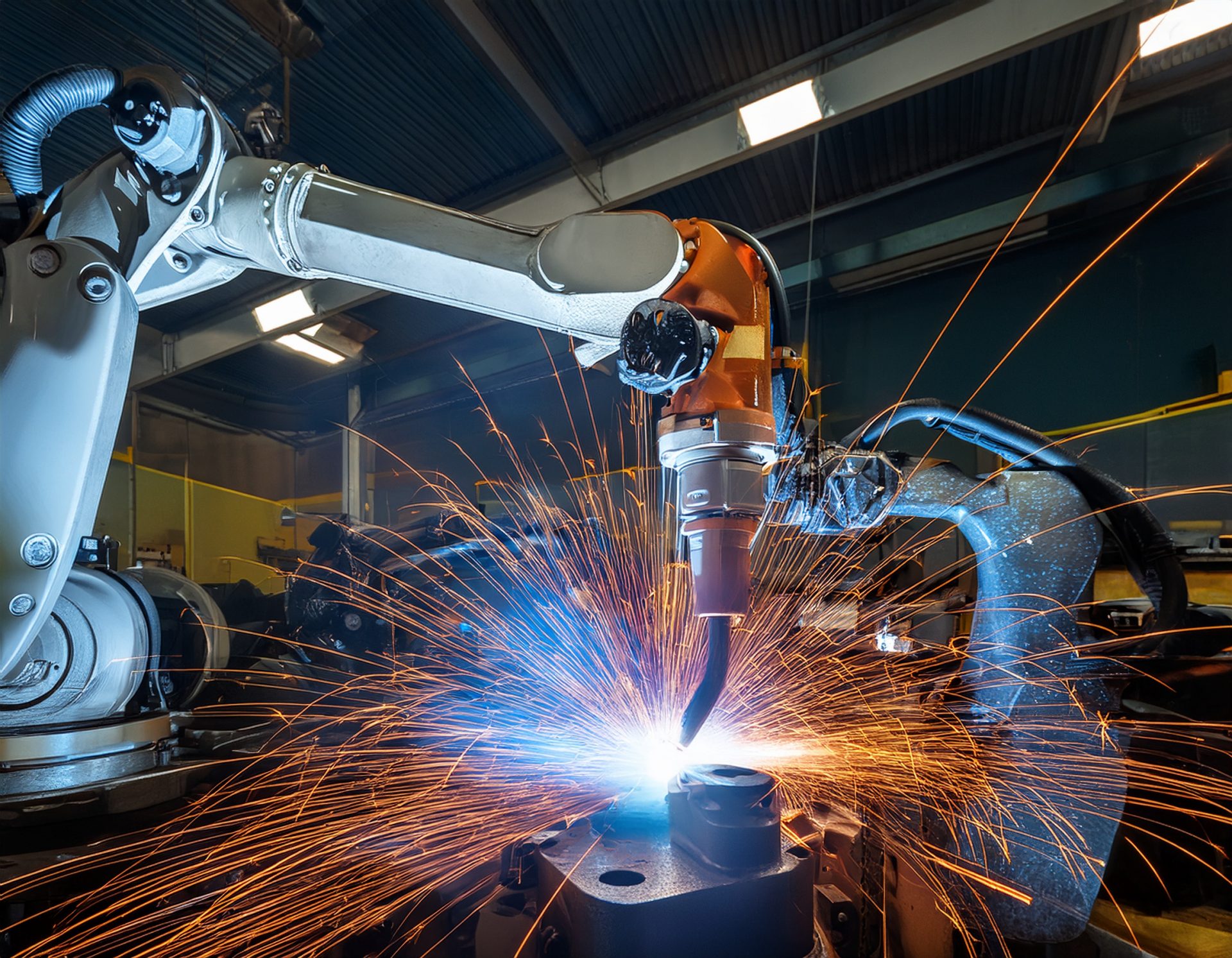
Benefits of Robotic Welding
- Increased Efficiency: Robots can work continuously without breaks, optimizing production.
- Consistency & Precision: Robots ensure uniform welds with minimal errors, unlike manual welding.
- Improved Safety: The welding process requires high heat and hazardous fumes. Using robots reduces human exposure to these conditions.
- Lower Costs in the Long Run: Initial investment in this technology is high, but automation reduces labor costs and minimizes waste.
- Versatility: Robots offer adaptability to a wide range of techniques, materials, and applications, making them valuable in many industries.
- Better Weld Quality: Advanced systems can detect inconsistencies and adjust, ensuring higher quality results.
Drawbacks of Robotic Welding
- High Initial Cost: Purchasing and setting up of a robotic welding system requires a significant investment.
- Programming and Maintenance: These systems require skilled technicians for programming and maintenance. And periodic calibration is also a requirement.
- Job Displacement: While automation can increase production, it reduces the demand for manual welders, leading to concerns about job security.
Industries That Use Robotic Welding
Many industries have adopted and rely on robotic welding for mass production and precision work. Some of which include:
- Automotive: Used in the assembly of vehicle frames, exhaust systems, and other components. Delivering strong, reliable joints in car bodies that improve durability and safety.
- Aerospace: Ensures high-strength welds for aircraft structures, jet engines, and other aerospace components, where precision is critical. Helping reduce material waste and increasing the structural integrity of parts.
- Construction & Infrastructure: Used in building bridges, pipelines, heavy machinery, and structural frameworks for buildings to ensure durability and strength. Large-scale projects can benefit from the speed and accuracy of robotic welding.
- Medical Equipment: Used in the manufacturing of surgical tools, implants and high-tech medical devices that require clean, precise welds. The demand for flawless welds in medical applications makes robotic welding an essential technology.
- Shipbuilding: Large -scale welding applications in ship hulls and superstructures, where robots handle repetitive, labor-intensive welding tasks. Robotic welding delivers consistent and strong welds, reducing the risk of structural failure.
Types of Welding Used in Robotic Systems
Robotic welding lends itself to a variety of welding techniques that vary depending on the application. Some common types include:
- Arc Welding: Electricity is used to generate an arc that melts materials to create a strong bond.
- MIG (Metal Inert Gas) Welding: A wire electrode and shielding gas creates high-quality, efficient welds.
- TIG (Tungsten Inert Gas) Welding: Precise welding for delicate and high-quality welds, often used for aluminum and stainless steel.
- Spot Welding: A technique that joins metal parts using heat and pressure, common in the automotive industry.
- Laser Welding: An application using a laser beam for extremely precise and clean welds. Commonly used in electronic and medical device manufacturing.
- Plasma Welding: Precise, high-energy welding. Ideal for aerospace and micro-welding applications.
Training Skills and Requirements
While robotic welding reduces the need for manual welding, skilled workers are still required to set up, program, and maintain these systems. Training includes:
- Understanding robotic systems and programming languages.
- Learning welding techniques and safety protocols.
- Troubleshooting and maintenance of the equipment.
- Quality assurance techniques to ensure optimal weld strength and consistency.
Certifications in robotic welding are available from organizations like the American Welding Society (AWS) and many vocational schools offer specialized courses in robotic automation. Many companies also offer in-house training programs to develop skilled robotic welding technicians.
The Future of Robotic Welding
With advancements in artificial intelligence, machine learning, and sensory technology, robotic welding is becoming smarter and more adaptable. In the future, innovations could include:
- Increased Use of AI: Robots can learn from experience and adjust in real time.
- Improved Collaboration with Humans: Cobots (Collaborative Robots) to work alongside human welders for complex tasks.
- More Affordable Solutions: With evolving technology, costs can become more accessible to smaller businesses.
- Advanced Sensing and Quality Control: Sensors and AI-driven inspections can ensure near-perfect welds with minimal defects.
- Sustainable Welding Systems: New methods can reduce energy consumption and emissions in welding processes.
- Remote Monitoring & Automation: Cloud-based monitoring systems to track and adjust robotic welding operations in real time, reducing downtime, and improving efficiency.
- 3D Printing Integration: A combination of robotic welding and additive manufacturing can lead to the development of complex structures with minimal material waste.
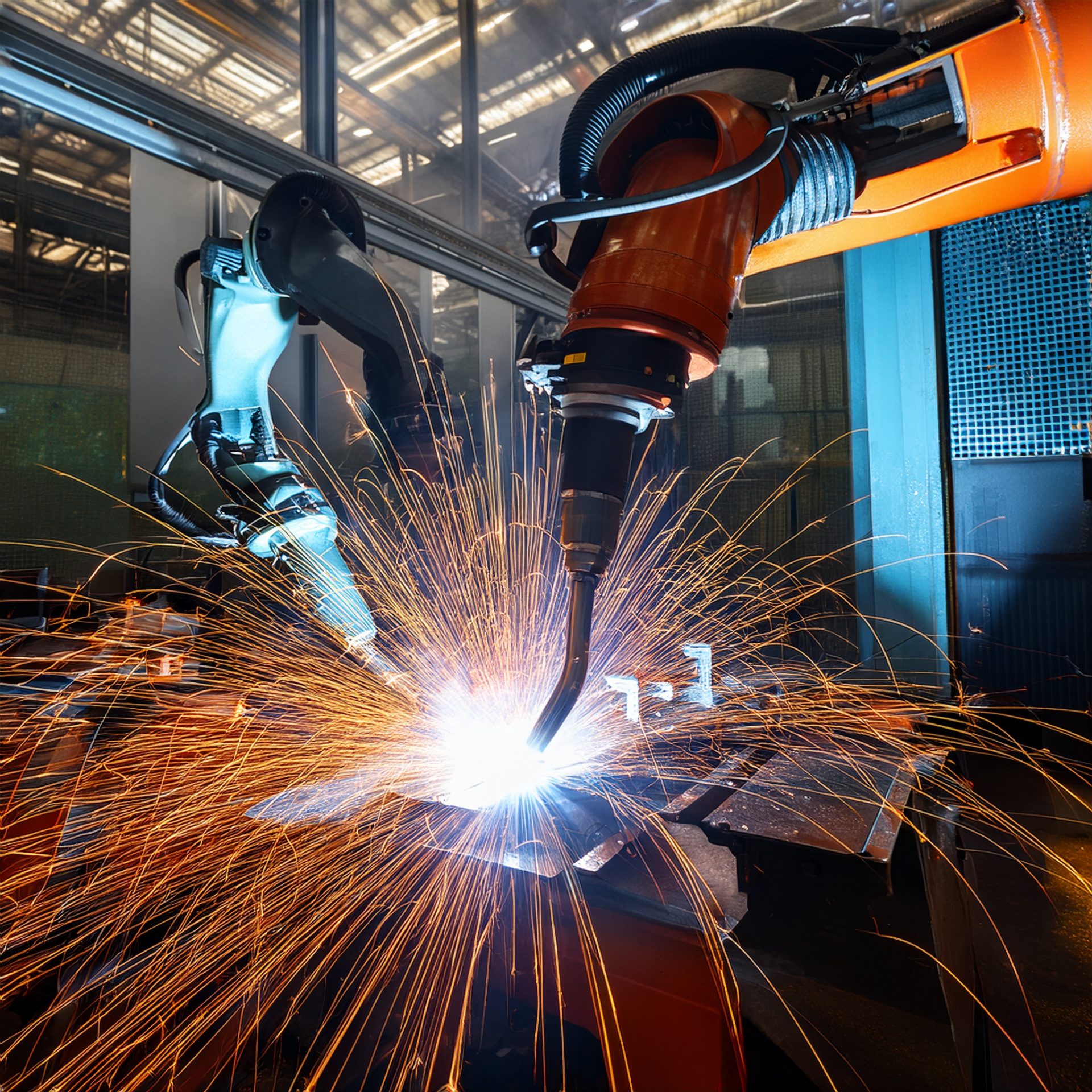
All in All
Robotic welding is transforming the manufacturing landscape by increasing efficiency, precision, and safety. While it comes with an initial investment and requires skilled technicians, the long-term benefits far outweigh the drawbacks. As technology continues to evolve, robotic welding will become more integral to industries worldwide. Whether manufacturing, construction, or automotive production, robotic welding is shaping the future of industrial fabrication.
About Suburban Welding & Steel
We are an experienced shop that has served Chicago and its suburbs since 1952. Delivering tailored welding solutions to companies and individuals across many industries. Offering versatile, dependable solutions for every project.
Beyond welding services, we offer a wide range of capabilities, which include:
- Plate rolling.
- Plate shearing.
- CNC Machining.
- CNC forming.
- General and custom fabrication.
- Heavy-equipment repair.
- On-site solutions.
- Raw material sales.
- And more!
Work with us to take any project from concept to completion. We make every step simple and deliver the results you need!
Whether in one of our shops or on-site, we provide the support and solutions you need!
Work With Us!
To learn more about how we can serve you, please call 847-678-1264. There, you can speak with one of our knowledgeable representatives. They can discuss your needs in more detail and can provide more information about our capabilities. If you would prefer to send us a message, please fill out the form found on this page, and we will contact you as soon as possible.